Pulp and Paper
Metals have myriad effects on the pulp and paper process, both in machinery maintenance and in purity and quality of product.
Metals like iron, manganese and copper can have effects on the bleaching process which can darken the paper, reducing quality and directly affecting the value of the final product.
Metals can enter the process from the source water, which may not be consistently pure enough for your process, a fact we can confirm with continuous input water monitoring. Metals can also increase throughout process due to some additives required for other processes. For example, alum has been known to contain iron in some cases, leading to deleterious effects. In addition to in water sources and required process additions, metals can get into the process from the wood itself, which can contain iron, manganese, copper, aluminum, calcium, and magnesium. Zinc, cobalt and barium have also been found in wood on occasion, depending on the source of the lumber.
Having the data you need to respond to changes in your water quickly is vital for pure, white paper that generates the most revenue. Our sensors can help you achieve these goals.
Most common metals found in the Pulp and Paper Industry
- Iron
- Copper
- Manganese
- Aluminum
- Calcium
- Magnesium
- Zinc
- Cobalt
- Barium
Different Applications for the Sensor
Process Optimization
Knowing the concentration and ratios of metals in process fluids in real time is vitally important for process optimization and the production of pure white paper. The removal of metals in and in between processes can increase process efficiency and
Effluent Monitoring
Metals that escape through process can result in environmental fines and can risk site closures. Pulp and paper processes cause quick variation in waters, meaning that realtime monitoring is the only real solution to this issue. By catching these metals before they cause problems, facilities can save money through fines, overdosing of chemicals, and through man hours tied up in testing.
Machinery Maintenance
The metals running through your vital machinery have massive effects on the life of your machinery. Maintaining essential systems like boilers requires proper pre-processing. Knowing what is in the water before it reaches your systems and knowing the efficacy with which you are cleaning that water are essential tasks.
How the AquaValid Works
Aquavalid takes a small slip stream from the water flow, converts it to a plasma and records the spectral information from the plasma at about 5000C. At these temperatures most metal contaminants in the water start to glow. The raw data is reported to a cloud computing environment that analyzes the spectral information to determine the contaminants and quantity of each contaminant. The larger the quantity of a metal in the source water, the brighter that metal is in the generated light. This information can be reported to the SCADA systems controlling chemical injection to optimize the treatment. It is also stored and available as a report of graph of each contaminant, or groups of contaminants for regulatory reporting, historic analysis for planning purposed or other needs. Where multiple clients share a watershed the client may elect to share the information with clients downstream to provide advanced warning of changes in the source water.
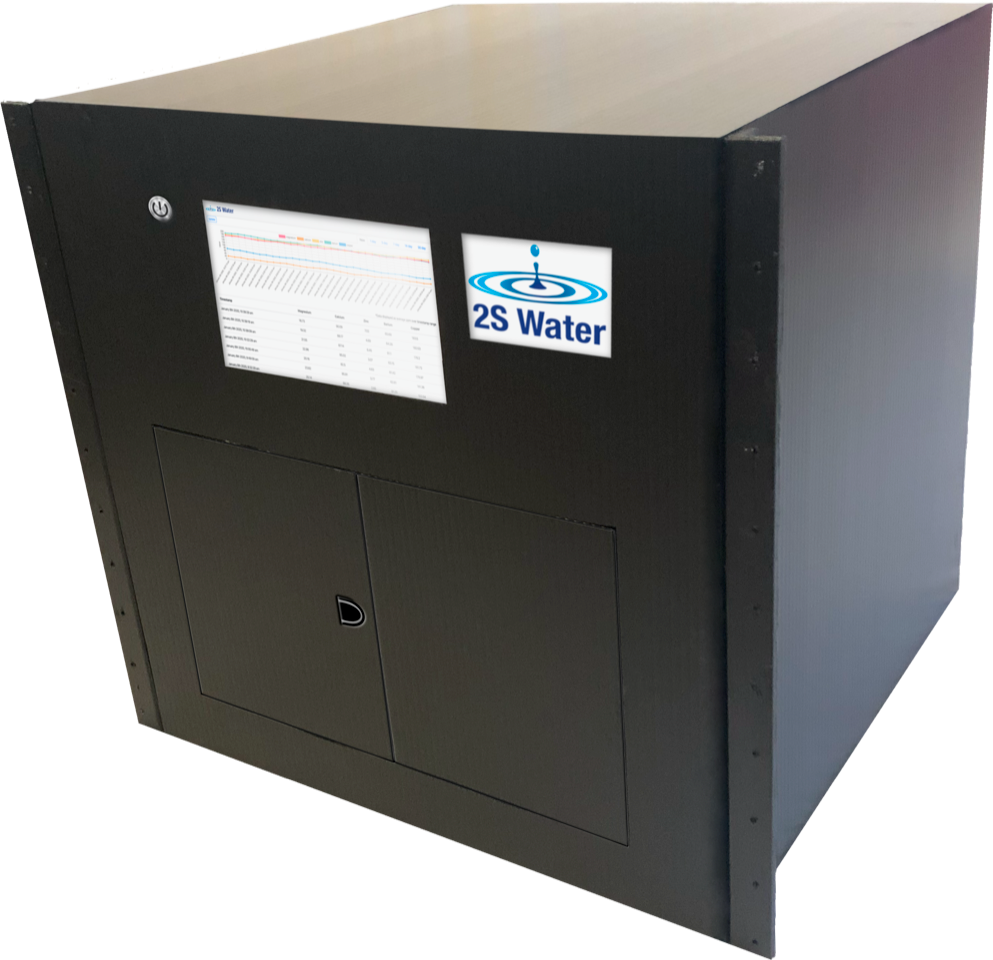